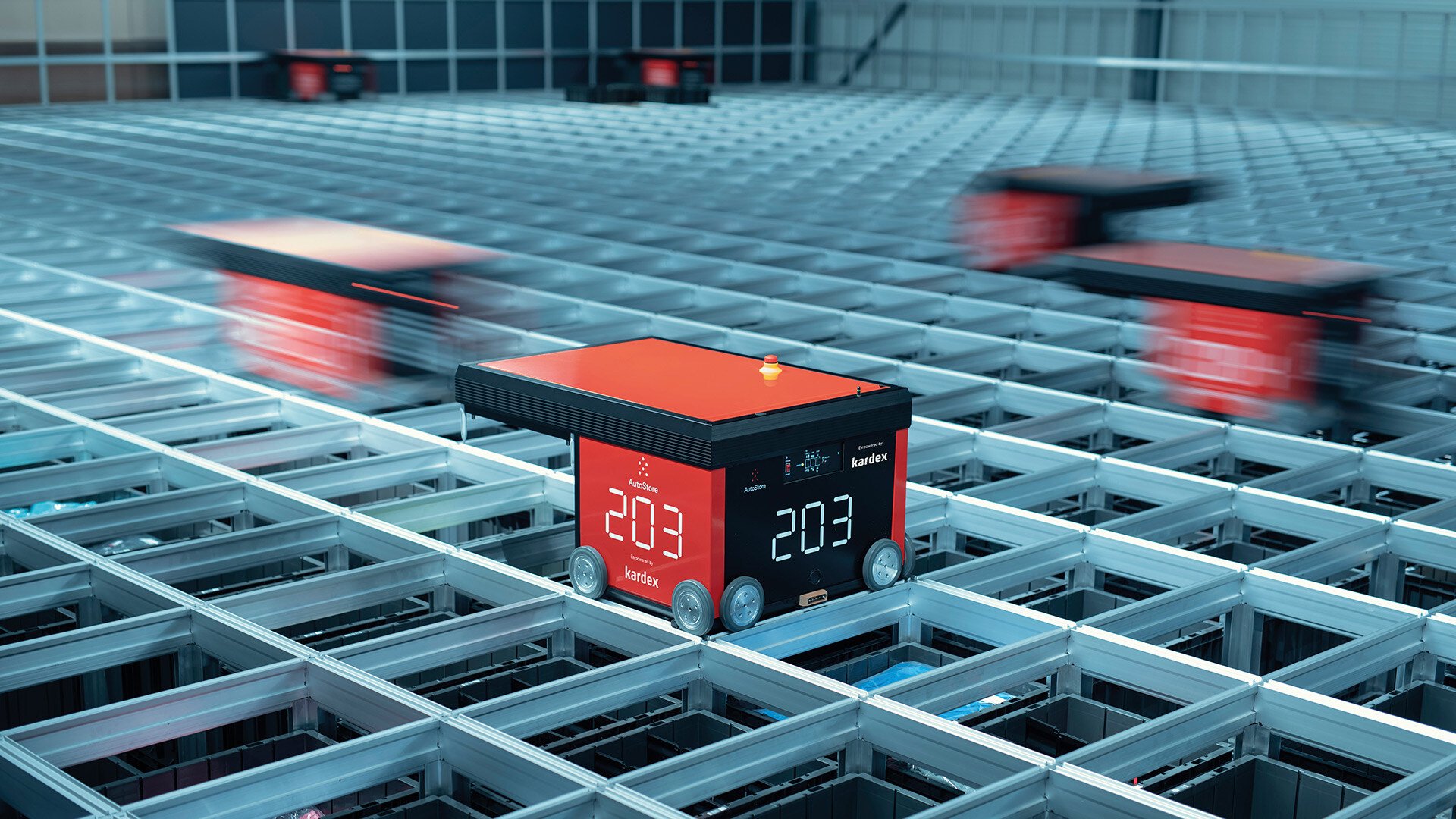
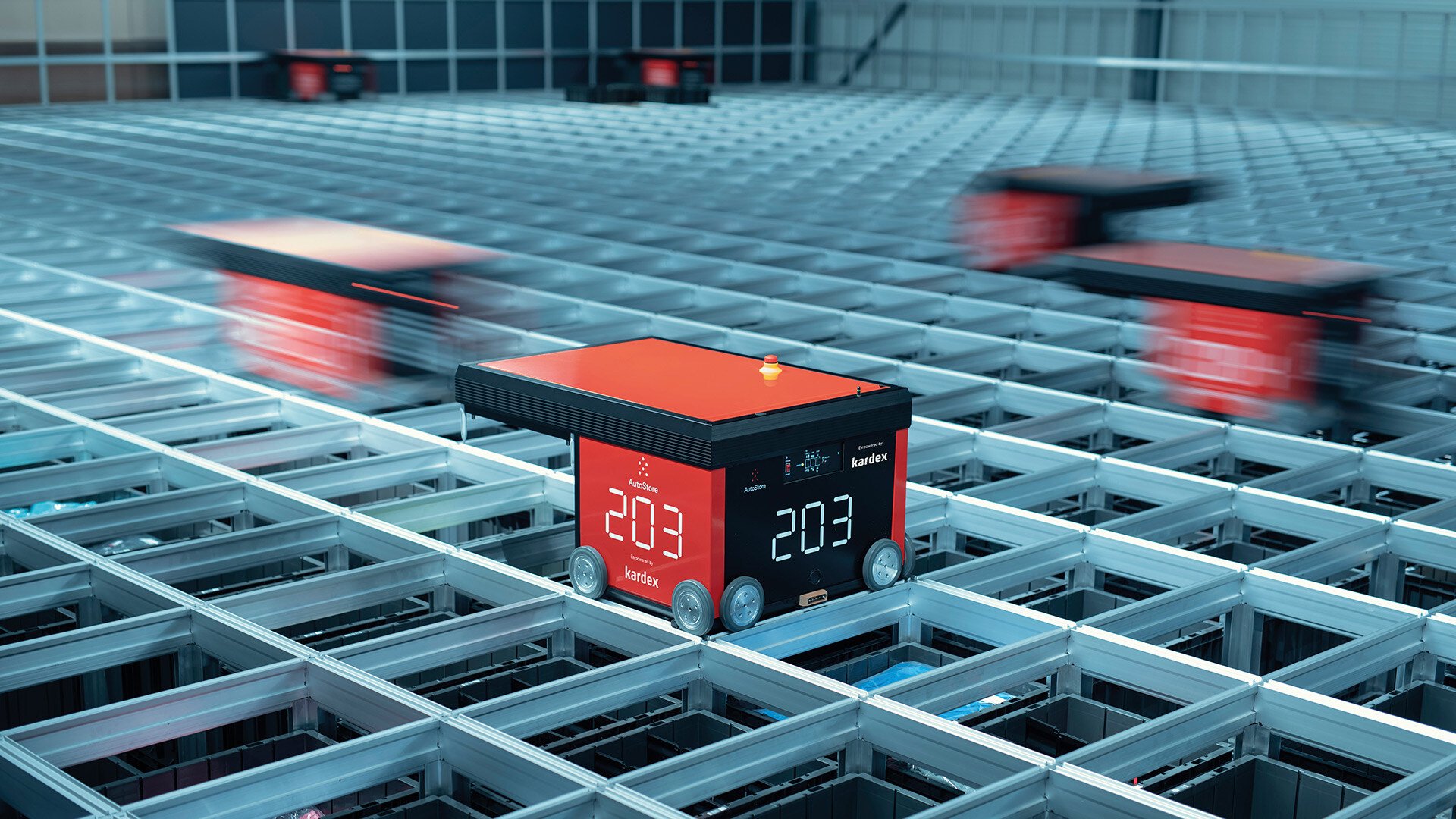
Omni-Channel Apparel Order Fulfillment Streamline order fulfillment across online and in-store channels, enhancing efficiency and customer satisfaction
Watch Case StudyOptimize your storage space utilization, inventory retrieval, and picking operations with AutoStore empowered by Kardex.
-
Increase storage capacity
by up to 400% within your existing footprint—no need to relocate or expand your facility.
-
Improve picking efficiency
with the fastest ASRS per square foot.
-
Access returned items immediately
with automated return management and the elimination of shelf restocking.
-
Enable same-day shipping
with fast, single-minute order fulfillment via the Kardex FulfillX.
-
Optimize storage layout
with the elimination of picking walkways.
-
Lower labor costs
AutoStore requires significantly fewer picking operators compared to manual processes.
Increase storage capacity
by up to 400% within your existing footprint—no need to relocate or expand your facility.
Improve picking efficiency
with the fastest ASRS per square foot.
Access returned items immediately
with automated return management and the elimination of shelf restocking.
Enable same-day shipping
with fast, single-minute order fulfillment via the Kardex FulfillX.
Optimize storage layout
with the elimination of picking walkways.
Lower labor costs
AutoStore requires significantly fewer picking operators compared to manual processes.
Case Study: Cutter & Buck
Cutter & Buck Faced Challenges During the Pandemic
The journey toward automated order picking at Cutter & Buck’s fulfillment center in Washington began during the pandemic when their legacy pick module struggled to meet growing demands. During peak seasons in 2020 and 2021, surging e-commerce sales, coupled with labor shortages, pushed leadership to step in and assist with order fulfillment directly. This included contributions from sales representatives, the CFO, and CEO Joel Peter Freet, who all worked shifts in the three-level pick module to help process orders.
Recognizing the Need for Change
These experiences highlighted the need for a more efficient, long-term solution that could handle peak demand while streamlining supply to embroidery machines on a near just-in-time basis.
“We all pitched in, getting trained on our picking processes and committing to multiple shifts per week during the holidays,” Freet recalls. “By holiday 2021, our e-commerce was growing so fast we had no choice but to pitch in again. During our post-mortem, we explored ways to make the existing processes more efficient, including changing the layout of the picking module, or possibly reducing SKUs. In the end, we uncovered that to keep up with our growth, we would need a breakthrough in productivity to support our peak season sales in the future, and that’s what brought us to looking at next-generation picking automation systems.”
Customization and Dual Workflows
Cutter & Buck, a Seattle-based omnichannel retailer of activewear and lifestyle apparel, services North America through three distribution centers. The Renton facility specializes in customized apparel, utilizing advanced embroidery machines, with customization driving nearly half of its picking activity. As a result, the DC must manage two workflows: fulfilling non-customized apparel orders for direct-to-consumer sales or retail outlets and picking items to supply embroidery operations.
Finding the Right Automation Solution
The company’s leadership identified bottlenecks in the manual picking processes and explored automation options, including mobile robots. They concluded that replacing the pick module with a high-density automated storage and retrieval system (AS/RS) would be the most impactful solution.
The AutoStore system, empowered by Kardex, went live in August 2023, operating with Kardex’s FulfillX warehouse execution system (WES).
Seamless Integration and Immediate Impact
This implementation included integration between the WES and Cutter & Buck’s warehouse management system (WMS) using SVT Robotics’ orchestration software to streamline processes such as replenishment and order waving. The results exceeded expectations: during peak season, 12 associates working with AutoStore managed volumes that previously required 30 workers.
“The solution has absolutely helped us with our picking efficiency,” says Sumpter. “We are not only shipping same day for blank orders consistently with no real challenge, now we’ve been able to reduce our time for embroidery processes, allowing faster turns there. It is because the AutoStore system is getting orders out to shipping, or to embroidery, very quickly.”
Goods-to-Person Efficiency
AutoStore’s goods-to-person (GTP) principle keeps pickers stationary at ports while robots retrieve totes from the high-density storage grid and deliver them to workstations. This eliminates travel time within the warehouse, enabling faster and more accurate picks. The intuitive software interface and visual guidance make training efficient; associates can be productive within 10 minutes.
“We can teach people to be productive pickers in about 10 minutes, and a good part of that is safety protocols we go through,” says Sumpter. “We are working to get almost everyone, though not our embroidery machine operators, trained on AutoStore so we can move people around fluidly.”
Designed for Future Growth
The Renton AutoStore system, with 11 ports, 54 robots, and over 34,000 bin positions, was designed to handle five years of growth. It supports direct-to-consumer orders by picking items directly into shipping cartons, while goods for embroidery are picked into totes and staged near production areas for immediate use. The system’s dense storage capacity has also allowed Cutter & Buck to repurpose a former three-day work-in-progress staging area for miscellaneous storage.
Meeting Peak Season Demands
The deployment’s primary goal was to eliminate bottlenecks and enable more efficient labor allocation rather than just reducing headcount. The implementation resulted in improved service levels and faster order fulfillment across all channels.
“I think our ability to commit to the fastest service levels that we possibly can has been really positive for the company,” says Sumpter. “Our AutoStore deployment has been critical to removing the bottleneck in picking that was previously challenging our ability to hit those high service levels year-round.”
Looking Ahead with Confidence
“The big objective was to remove the bottleneck from picking, so we could really make significant leaps forward in our efficiency and therefore capacity throughout our decoration and fulfillment operation,” Freet says. “Enabling a faster turn to our customer while improving our efficiencies was the long-term objective. We have several years of growth still in front of us with the same base system, so I’m confident that we can continue to improve the rest of our operations and keep deliveries super-fast by utilizing the AutoStore system better and better.”
Is AutoStore right for you?
Why partner with Kardex?
-
Dedicated project management
Kardex has dedicated project managers committed to working side by side with you through system concept, design and installation.
-
Guaranteed installation & ramp up support
We don't leave after your AutoStore system goes live. We will be onsite during the installation and ramp up phase to ensure a smooth transition for you and your team.
-
Local ongoing support & maintenance
Using our extensive nationwide service and support network, you'll be fully supported throughout the lifecycle of your AutoStore system, even in the most remote location.
Dedicated project management
Kardex has dedicated project managers committed to working side by side with you through system concept, design and installation.
Guaranteed installation & ramp up support
We don't leave after your AutoStore system goes live. We will be onsite during the installation and ramp up phase to ensure a smooth transition for you and your team.
Local ongoing support & maintenance
Using our extensive nationwide service and support network, you'll be fully supported throughout the lifecycle of your AutoStore system, even in the most remote location.